Butt Weld Design [Structural Calculation]
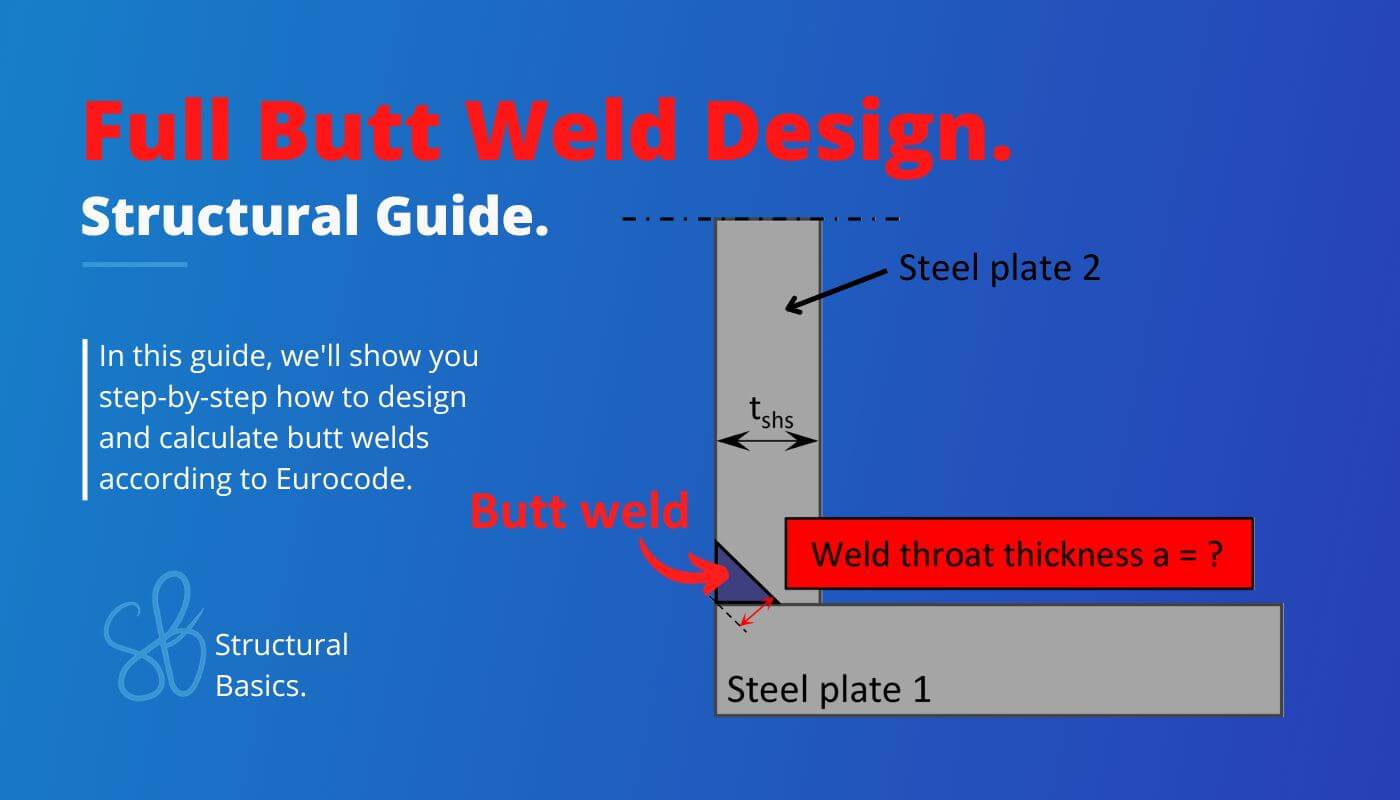
Butt welds are one of the most common types of welds.
In this article, we’ll show you step-by-step with an example structure how to design and calculate them.
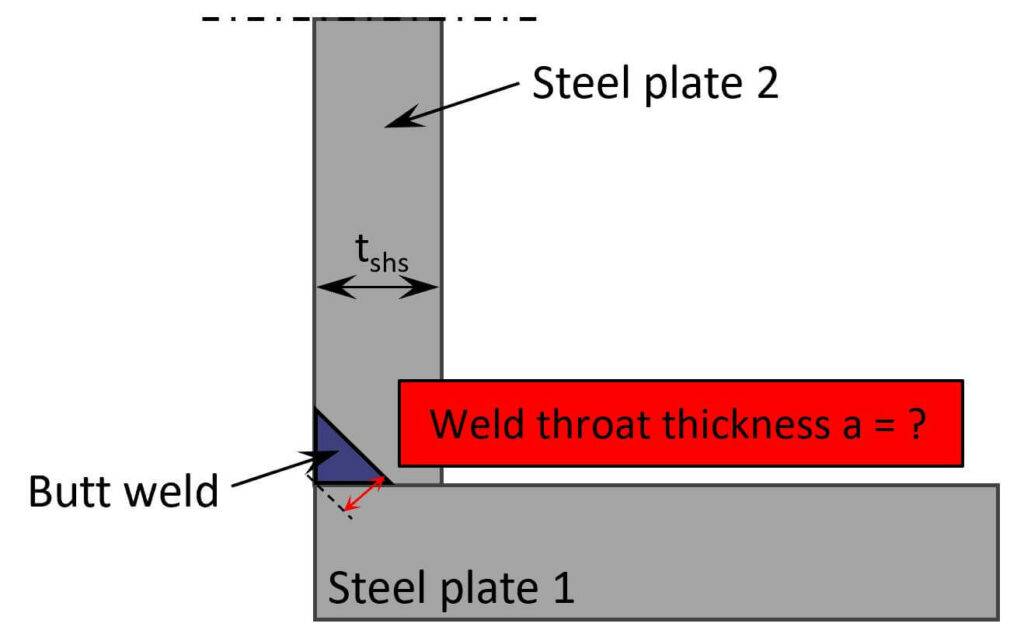
So let’s get started.
The Type Of Butt Weld
According to Eurocode EN 1993-1-8 4.7 there are 3 different types of butt welds. We’ll describe the procedures for these 3 in the following.
Full Penetration Butt Welds
EN 1993-1-8 4.7.1 (1) says that the resistance of a full penetration butt weld is equal to the resistance of the weaker of the 2 parts the butt weld connects. This applies as long as the tensile and yield strength of the weld are not less than the one from the parent metal/steel.
This means that when the (full penetration) butt weld connects a steel plate of strength class S235 and another one of class S355, the butt weld has to have the strength class S235.
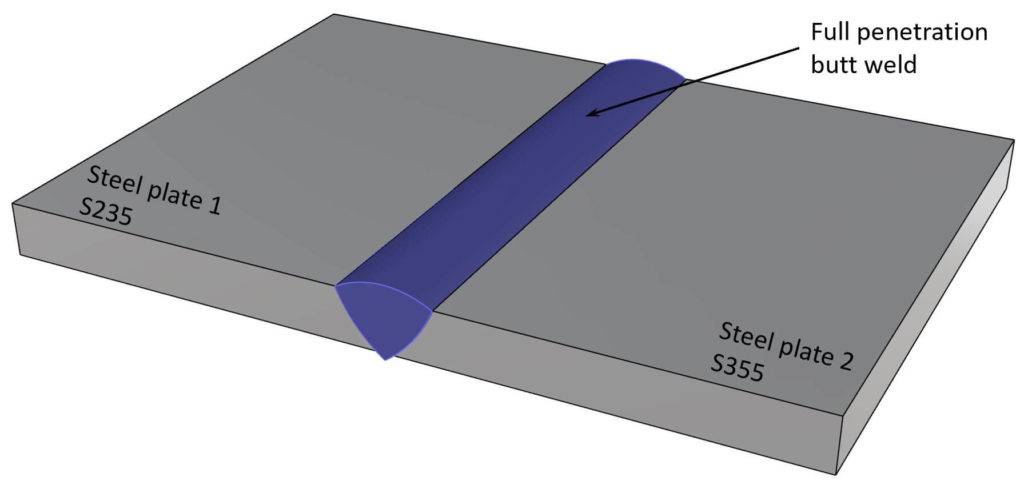
For us engineers, this means that we don’t have to verify the butt weld, and we can refer to EN 1993-1-8 4.7.1 (1). Only the steel plates have to be verified.
Here are more examples of full penetration butt welds. 👇👇
Single bevel butt weld

Square V butt weld

Single J butt weld

Partial Penetration Butt Welds
A partial penetration butt weld is a weld which doesn’t penetrate the full thickness of the 2 metals joined together. The picture below illustrates an example.
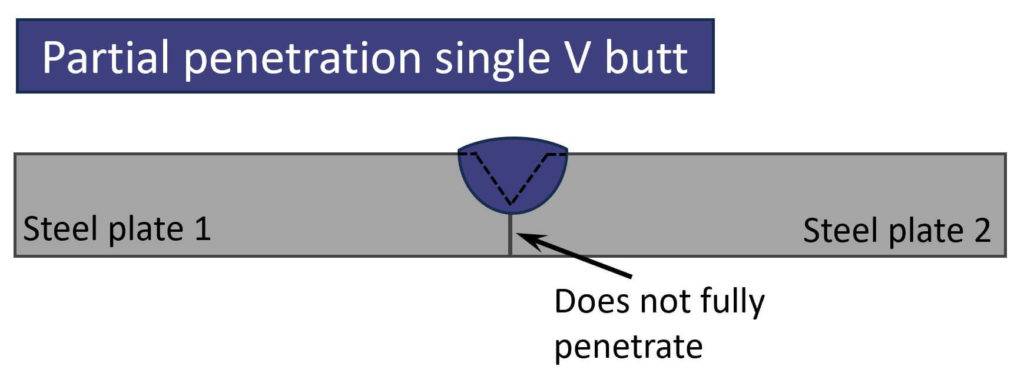
According to Eurocode EN 1993-1-8 4.7.2 (1) are partial penetration butt welds designed as deep penetration fillet welds.
This means that the guidance for fillet welds (EN 1993-1-8 4.5.3) is followed, but the throat thickness of a deep penetration fillet weld is used (EN 1993-1-8 Figure 4.4).
Eurocode proposes two methods to design fillet welds and in our case partial penetration butt welds:
- Directional method (EN 1993-1-8 4.5.3.2)
- Simplified method (EN 1993-1-8 4.5.3.3)
Later in this article, we show step-by-step how to calculate a partial penetration butt weld using the simplified method.
T-Butt Joints
T-Butt joints are a type of butt weld which connects a perpendicular piece of metal to another metal. The weld can exist of 2 partially penetrated butt welds, a fully penetrated butt weld or 1 partially penetrated butt weld.
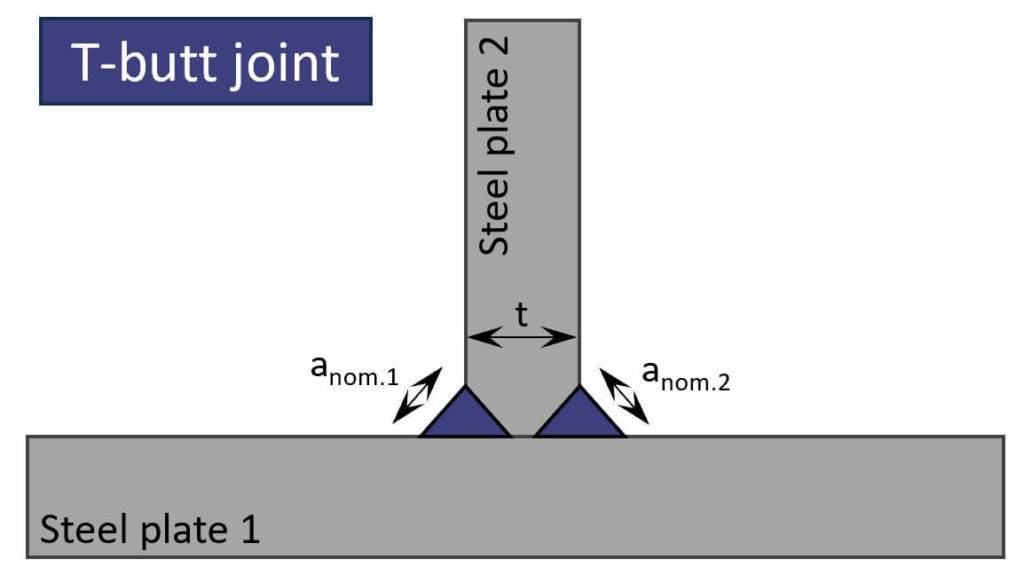
A T-butt with 2 partially penetrated butt welds as in the picture above is categorized as a fully penetrated butt weld if anom.1 + anom.2 > t.
1 partially penetrated butt weld and 2 partially penetraded butt welds with anom.1 + anom.2 < t are calculated as fillet welds.
Example Calculation Of A Partial Penetration Butt Weld
As already mentioned earlier in the post, we are now verifying a partially penetrated butt weld.
For the following example structure, a butt weld makes most sense, because a fillet weld could only be used on the top and bottom flanges. Depending on the loads, these 2 fillet welds might not verify.
Whereas, a partially penetrated butt weld can be used all around the cross-section of the SHS profile.
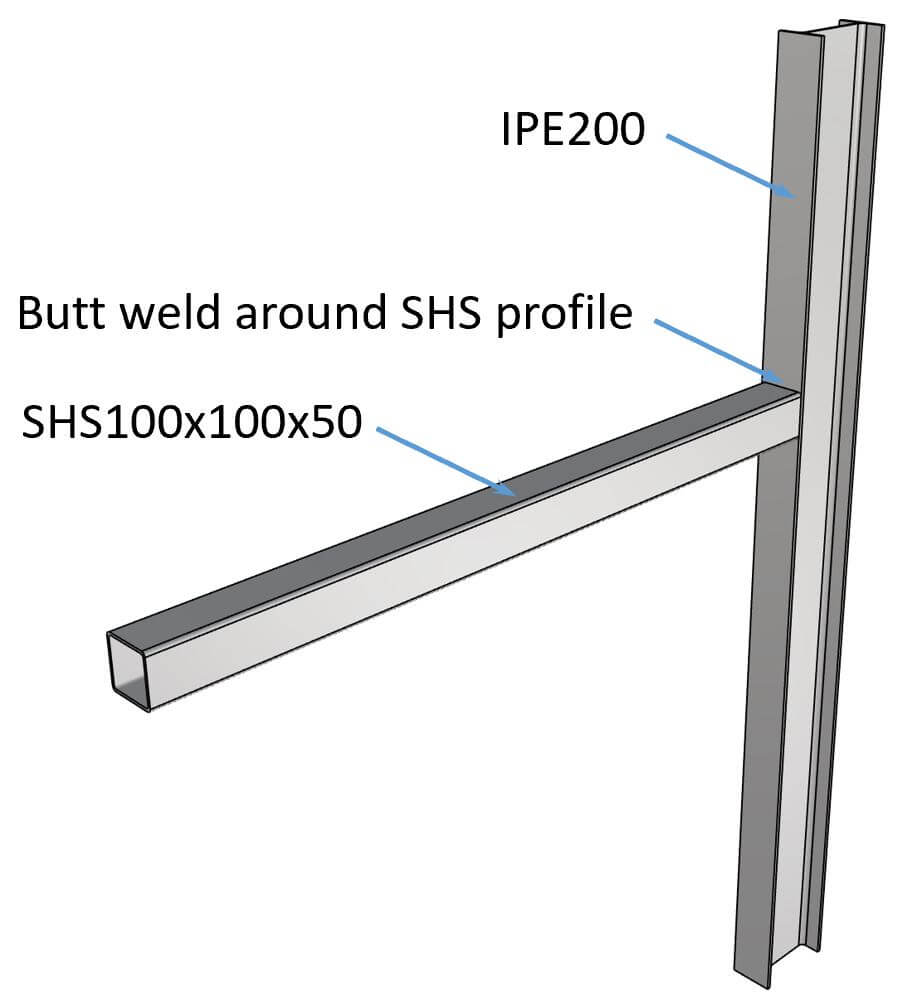
Loads/Internal forces
We calculate the butt weld for the following internal forces:
Design bending moment | $M_{d} = 5 kNm$ |
Design axial force | $N_{d} = 8 kN$ |
Design shear force | $V_{d} = 2 kN$ |
Geometry of the butt weld
We decide to use a one-sided V butt.
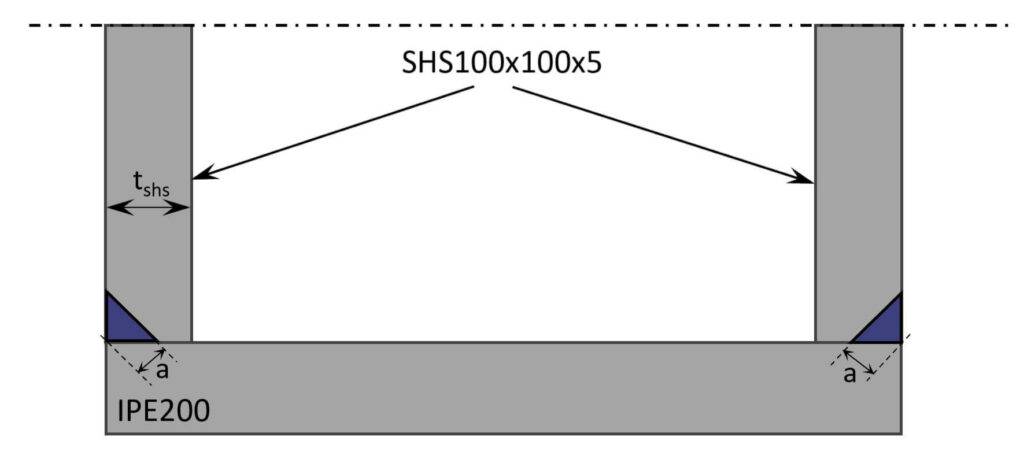
Throat thickness | $a = 3 mm$ |
Height SHS100x100x5 | $h = 100mm$ |
Width SHS100x100x5 | $w = 100mm$ |
Moment of inertia butt weld around SHS profile | $I_{y} = \frac{h^3}{6} +\frac{w^2 \cdot h}{2} = 2 \cdot 10^6 mm^4$ |
Section modulus | $W_{y} = \frac{I_y}{\frac{h}{2}} = 4 \cdot 10^4 mm^3$ |
Length of the weld | $l_w = 2h + 2w = 400mm$ |
Material data
Ultimate tensile strength | $f_{u} = 360 MPa$ |
Correlation factor (butt weld) | $\beta_{w} = 1.0$ |
Partial safety factor | $\gamma_{M2} = 1.35$ |
Verification
Max. stress in weld | $\sigma_{N} = \frac{M_d}{W_y} + \frac{N_d}{a \cdot l_w} = 132 MPa$ |
Shear stress | $\tau_{d} = \frac{V_d}{a \cdot l_w} = 1.67 MPa$ |
Resulting stress | $F_{w.d} = \sqrt{\sigma_{N}^2 + \tau_{d}^2} = 131.67 MPa$ |
Design resistance of weld (EN 1993-1-8 4.5.3.3) | $F_{w.Rd} = \frac{f_u}{\sqrt{3} \cdot \beta_w \cdot \gamma_{M2}} = 154 MPa$ |
Utilization | $\eta = \frac{F_{w.d}}{F_{w.Rd}} = 85.5 \%$ |
Conclusion
Et voilà, the butt weld is verified and dimensioned. 💯💯
That was a quick verification, wasn’t it?
If you are new to structural design, then check out more of our design tutorials where you can also learn how to design other steel, concrete and wood elements such as
But now, I would like to hear from you: Have you already designed a butt weld in university or at your work? Tell us a bit about the structure, as we all want to learn from each other.