What Is A Butt Weld? {Full Explanation}
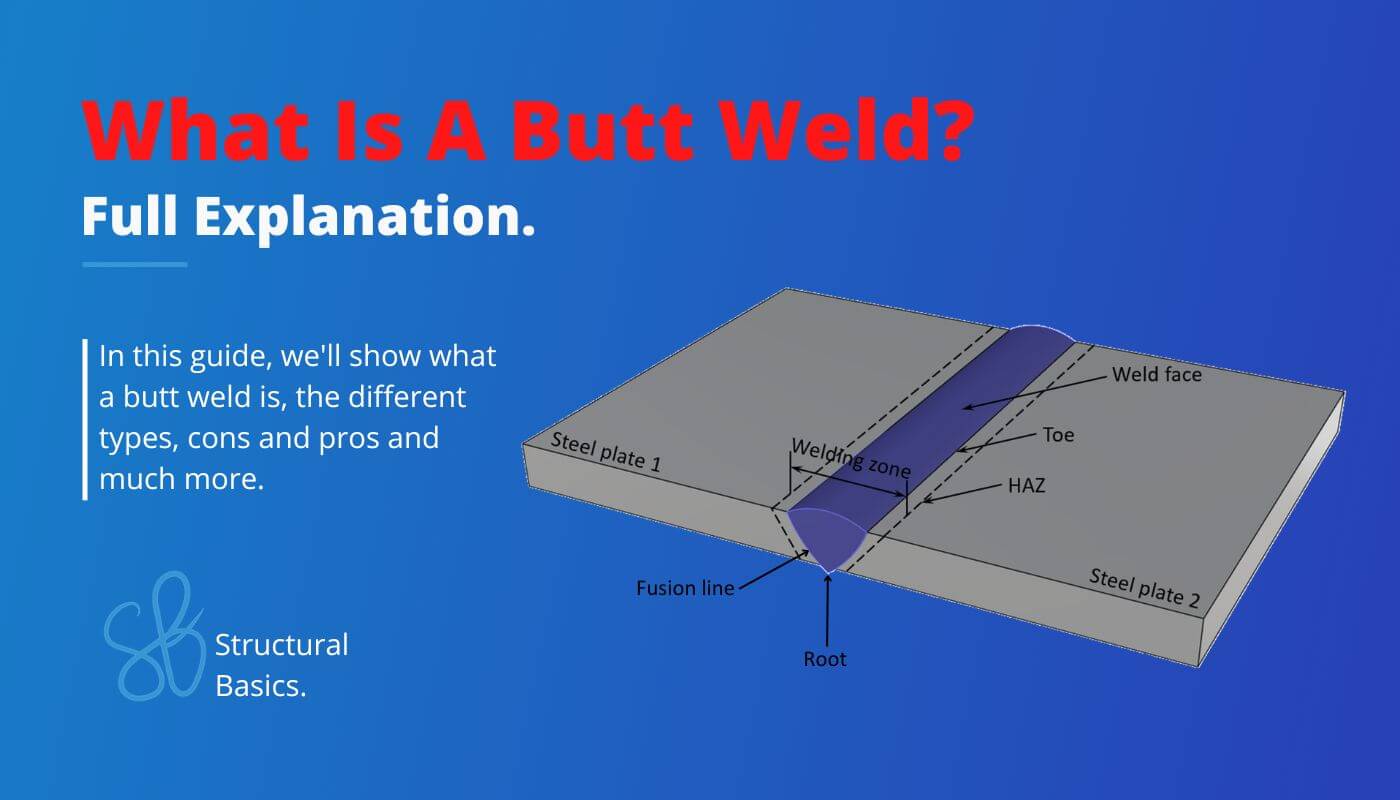
A butt weld is a welding technique where two metal pieces are joined together along their edges in a single plane. This creates a strong and seamless bond, commonly used in the construction, manufacturing, and automotive industries for its reliability and structural strength.
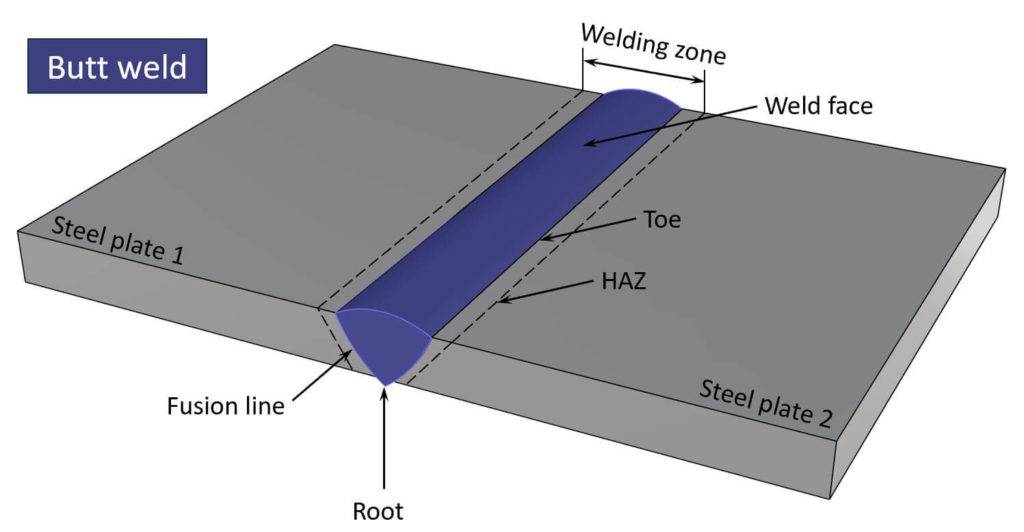
Later in this blog post, we’ll explain more in detail what a butt weld is, show the different types and applications of butt welds.ππ
We’ll also add real-world examples of steel structures with butt welds. ππ
Alright, let’s get into it. ππ
What Is A Butt Weld?
Butt welds are a popular welding method used to join two metal pieces such as steel plates along their edges in a single plane. When welding the 2 plates, the edges are first melted and then fused together to create a very robust bond.
Butt welds are great for structural steel connections, because a continuous/momentstiff connection is formed, which ensures that the joint retains the strength of the base material (steel beams/columns).
This welding technique is widely used in various industries due to its exceptional strength, durability, and cost-effectiveness. We’ll have a look at these industries later in the article. ππ
Types Of Butt Welds
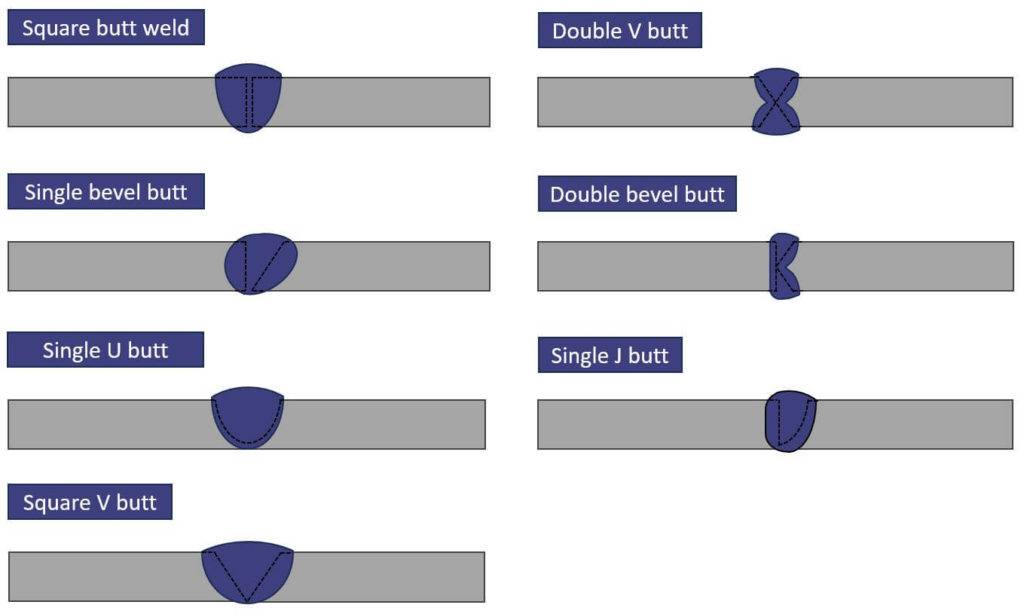
Square Butt Weld
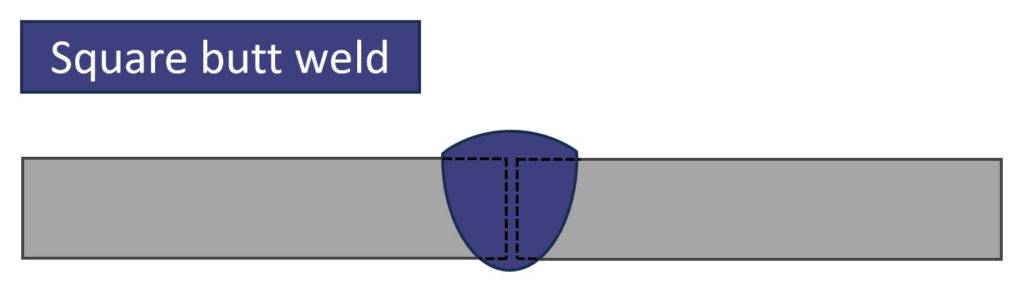
Single Bevel Weld
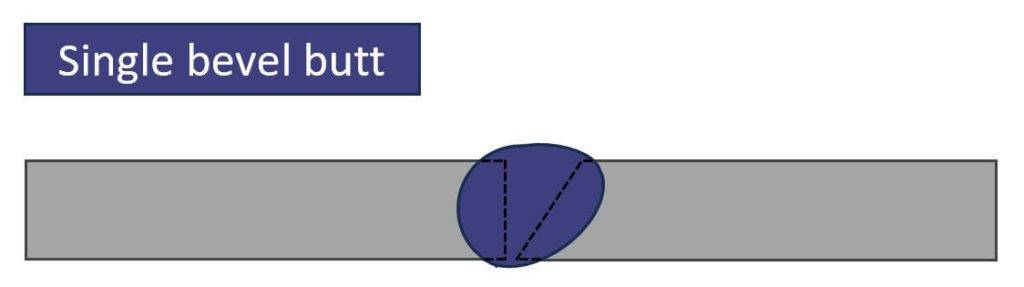
Single U Butt Weld
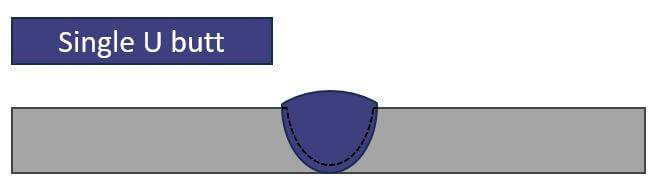
Square V Butt Weld
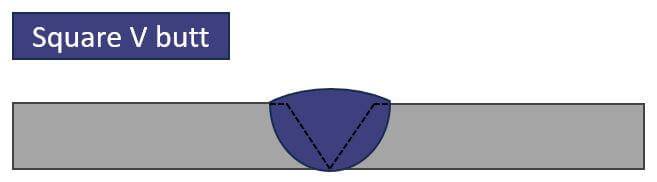
Single J Butt Weld
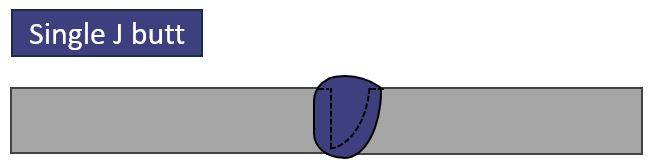
Double V Butt Weld
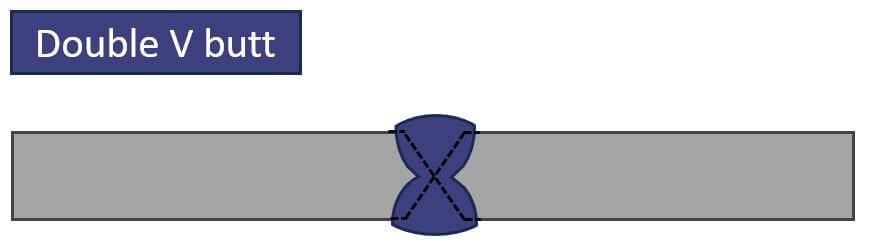
Double Bevel Butt Weld
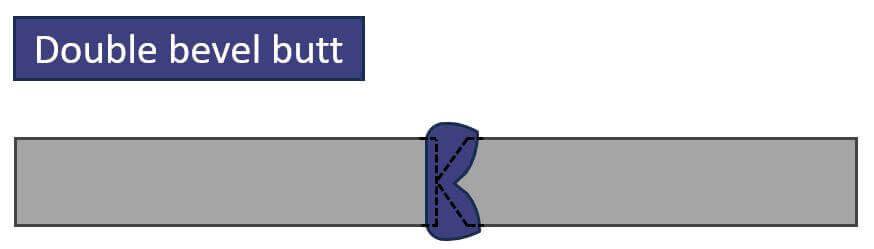
Process Of Butt Welding
Typically, the following step-by-step process is followed for butt welding. ππ
- Joint preparation
The edges of the metal pieces are cleaned from dirt, rust or contaminants. In this first step, it’s important that the edges are smooth for a good weld. - Welding setup
The welding machine is set up. Correct welding parameters, such as current, voltage, and travel speed are selected. - Tacking
Tack welds are used to temporarily hold the workpieces together. Here it’s important to check the alignment of the 2 plates. If needed, adjustments are made. - Welding
Heat is applied to the joint with the welding torch or electrode. The edges of the 2 plates are melting, and a molten pool is formed. - Weld progression
The welding torch/electrode is moved along the joint to fill the molten pool with the melted metal. Here it’s important to maintain constant speed. To avoid defects, overheating is avoided. - Cooling and Solidification
In this phase the welded joint cools naturally leading to a solidification of the molten metal. Excessive cooling rates lead to crack or other imperfections. - Post-weld treatment (optional)
Depending on the application and materials used, post-weld treatments like stress relieving or annealing can be considered. - Inspection and Finishing
Inspection of the weld for defects, such as cracks or lack of fusion. Finishing processes are performed to smoothen the surface and to achieve a desired appearance.
Here’s a good video showing how to weld a butt weld.
Example Of Butt Welds In Steel Structures
Moment stiff connection between IPE300 and SHS100x100x5 profiles
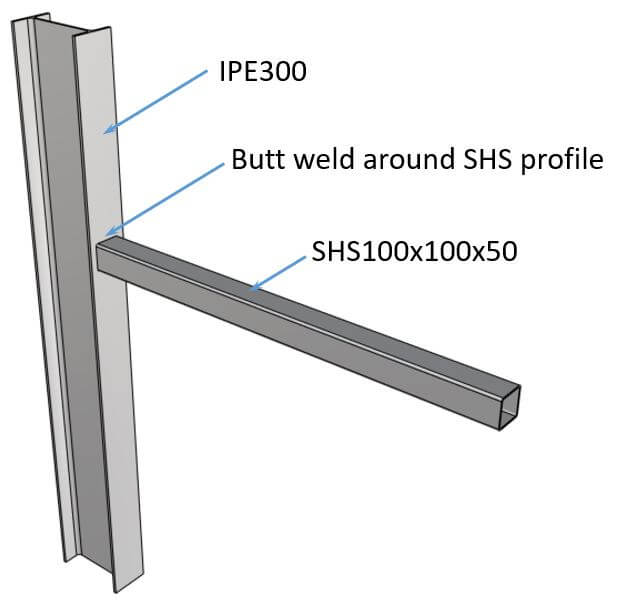
I personally had a similar connection as in the picture above where a fillet weld didn’t verify, because you can only weld from one side (the inside can’t be reached). I then used a butt weld, as it is stronger than the 2 profiles themselves.
Joining two steel profiles
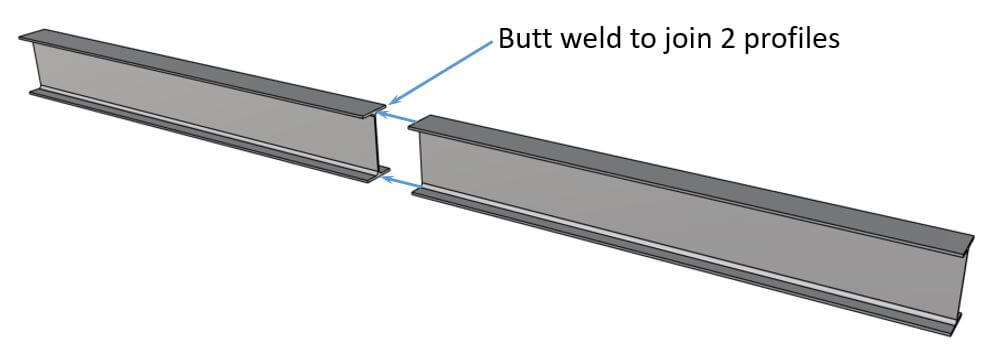
Butt welds are also commonly used to join two steel profiles with the same centerline. This can happen if long steel beams are required for a project, but only a certain length can be delivered due to a certain truck length.
Butt welds make sense in this case, because they don’t weaken the strength of the beam once the two pieces are joined together.
Pros And Cons Of Butt Welds
Pros ππ
- Strength: Butt welds have a higher strength than the base material (e.g. steel beams), if done correctly. This is unique as most connections are weaker than the profiles.
- Cost-effective: Butt welds are generally cost-effective as they require minimal additional materials. However, welding on-site can become quite pricy.
- Versatility: Butt welds can be used for all kinds of profiles and thicknesses.
Cons ππ
- Access limitations: In some cases, accessing the joint to do the weld is impossible.
- Susceptible to defects: If not executed correctly or if the base materials have impurities, butt welds can be susceptible to defects like cracks.
- Skill required: There are less and less skilled welders, making it challenging to find a contractor to perform the welding job.
- Time consumption: Proper preparation, including beveling or chamfering the edges can be time-consuming, especially for large projects.
Application Of Butt Welds
1. Construction industry
- Structural steel structures like warehouses or manufacturing plants: Here butt welds are used to join beams, columns, and other structural members together.
- Pressure vessels: Utilized for the fabrication of pressure vessels, such as tanks, boilers, and reactors. Butt welds are great for vessels, as the joints have to handle high-pressure and high-temperature environments.
- Offshore platforms (oil, gas or wind): Butt welds are employed to join components, such as steel jackets, decks, and bracings.
- Shipbuilding: Used for joining various sections of the hull, decks, and bulkheads. These welds are important for maintaining the structural integrity and seaworthiness of the vessel.
- Infrastructure projects: Used in various infrastructure structures, including tunnels, steel bridges, viaducts, and elevated roadways.
2. Manufacturing sector
- Machinery fabrication: Used in the manufacturing of industrial machinery, such as metalworking machines, presses, and assembly equipment.
- Electronics and electrical equipment: Butt welds are employed in the manufacturing of electrical enclosures, control panels, and various electronic devices.
- Appliance manufacturing: Butt welds are utilized in the production of household appliances like refrigerators, washing machines, and ovens.
- Consumer goods: Found in a wide range of consumer goods, such as metal frames for bicycles, exercise equipment, and household items.
3. Automotive and aerospace industry
- Chassis and Frame: Butt welds are used to join components of a vehicle’s chassis and frame, including the main structural rails, cross members, and subframes.
- Body Panels: Used in the automotive body construction to join sheet metal panels, such as the roof, door panels, and fenders. Butt welds result in a clean and seamless appearance, which is crucial for aesthetics and aerodynamics.
- Aircraft wings and wing components
- Engine Components: Employed in the assembly of engine components for an aircraft, such as exhaust ducts, engine mounts, and other structural elements.
Design Of Butt Welds
Butt welds are designed after the steel Eurocode 1993-1-8 4.3.4.
Check out our step-by-step design guide, where we show how you design butt welds according to Eurocode.
Conclusion
To summarize, butt welds are great to join two metal pieces, and they are much stronger as other welds like fillet welds. In fact, butt welds are as strong as the base material (the 2 metal pieces).
Now, that you got an understanding of butt welds, you can also learn about fillet welds and how to design them.
Usually before you design the welds, you design the steel members such as columns and beams, because you need to know their geometry and internal forces at the location of the connection.
I hope that this article helped you, and you know how to go further from here. In case you still have questions.
Let us know in the comments below. βοΈβοΈ
Butt Welds FAQ
Butt welds can be used to join metals like steel, stainless steel, aluminium, and copper, as well as thermoplastics and other materials used in the manufacturing and construction industries.
– high strength
– clean appearance
– cost-effectiveness
– versatility
A butt weld joins two pieces which are placed edge to edge, without any overlapping or gap between them. This makes the joint smoother and less visible compared to other types of welds like fillet welds, where the weld material is positioned at the intersection of two materials.